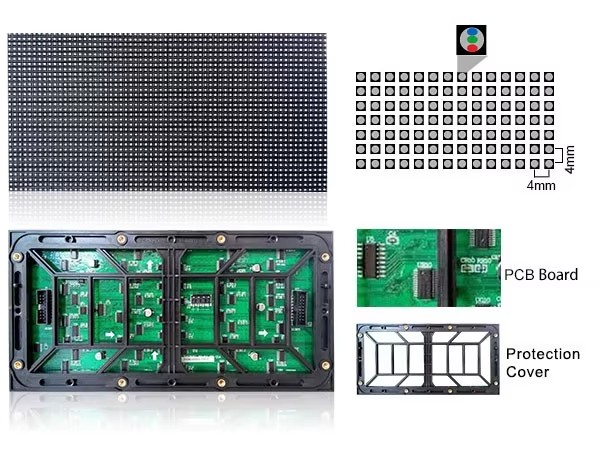
Basic skills for repairing LED display circuit boards
1. Understanding Capacitor Damage: Signs and Fixes
Capacitors, especially electrolytic ones, are among the most failure-prone components in LED display boards. Common signs of capacitor damage include:
- Reduced capacitance
- Complete loss of capacitance
- Leakage
- Short circuits
Pro tip: Visually inspect for bulging tops or leaked fluid, then verify using a capacitance meter or multimeter. Replacing damaged capacitors early can prevent larger circuit failures.
2. Identifying Faulty Resistors Accurately
Resistors rarely fail, but when they do, it’s usually due to an open circuit or increased resistance. Types like carbon film and fusible resistors are more prone to damage.
How to troubleshoot:
- Use a multimeter to measure resistance.
- Focus on high-value resistors—they’re more likely to fail.
- Wait for the reading to stabilize; capacitors in parallel may affect initial readings.
Note: If the measured resistance is higher than the nominal value, the resistor may be faulty. If it’s lower, it’s usually not a concern.
3. Testing Operational Amplifiers Without Removal
Operational amplifiers (op-amps) are commonly used in LED display control systems. You can check their condition in-circuit using the principle of virtual short.
In amplifier mode with negative feedback, the inverting and non-inverting inputs should be nearly equal in voltage (within millivolts).
If the voltage difference exceeds 0.5V, the op-amp is likely faulty.
In comparator mode, input voltages may differ significantly based on the logic level output.
Advantage: This method saves time and avoids unnecessary desoldering.
4. Easily Test SMT Components with DIY Needle Probes
Surface-mount components (SMT) are tiny and hard to test with standard multimeter probes.
Quick DIY fix:
Attach two fine sewing needles to your multimeter probes using thin copper wire and solder.
These needle probes can pierce through insulating layers for accurate testing without risking shorts.
5. Locating Power Supply Short Circuits
Power short circuits are tricky, especially when multiple components share a power rail.
Efficient method:
- Use a bench power supply with adjustable voltage/current (0–30V, 0–3A).
- Set voltage to match the circuit’s power supply and start with low current.
- Gradually increase current while feeling for overheating components—the hot one is likely shorted.
- Reminder: Never exceed voltage ratings or reverse polarity.
6. Fix Poor Contact with a Simple Eraser Trick
In industrial environments, dust and moisture can degrade contact points—especially gold-finger connectors on plug-in cards.
Solution:
- Rub the connector with a soft pencil eraser to clean the surface.
- Reinsert the card to restore good contact and avoid unnecessary replacements.
7. Diagnosing Intermittent and Environmental Faults
Some faults are not immediately obvious. These intermittent issues may be caused by:
Poor Contact:
- Loose plug-in cards
- Broken wires
- Cold solder joints
Signal Interference:
- External electrical noise or degraded component parameters
Poor Thermal Stability:
- Components like capacitors and ICs may behave differently when hot
Dust and Moisture:
- Can cause temporary conductivity, affecting performance during temperature changes
Software Margins:
- Narrow parameter settings in control software may trigger false alarms under normal conditions
Tip: Keep the board clean and consider re-flashing or updating software if necessary.
Conclusion
LED display doesn’t have to be daunting. By understanding component behavior, using smart diagnostic methods, and performing regular maintenance, you can effectively troubleshoot most issues without costly replacements. These 7 tips are practical tools to keep in your technician’s toolbox, whether you’re working on astadium screen or a commercial LED sign.